Table of contents
- What is inventory management?
- Why is inventory management important for businesses?
- Periodic vs perpetual inventory management—What's better?
- What are some inventory management challenges?
- How to create an inventory management plan
- 9 Essential inventory management techniques
- Best practices in inventory management
- Long-term inventory strategies
- Useful tools and technologies
- 4 Popular inventory management systems
- Leveraging business storage
What is inventory management?
Inventory management is the process of tracking and controlling your business’s stock and materials. It ensures you always have the right inventory available to meet customer demand without overstocking, which ties up cash and storage space. Effective inventory management balances the cost of holding inventory with keeping customers satisfied by fulfilling orders promptly.
5 Types of inventory stock
- Raw materials – The basic inputs used in the production process: wood for furniture, fabric for clothing, chemicals for pharmaceuticals, etc.
- Work-in-Progress (WIP) – Includes items that are not yet complete but are on their way to becoming finished products.
- Finished Goods – Finished goods that have gone through the entire production process and are stored until they are sold.
- Maintenance, Repair, and Operations (MRO) Supplies – Items used in the maintenance and repair of equipment and infrastructure, as well as operational supplies: lubricants, cleaning supplies, and office supplies.
- Packaging materials – Materials used to package and protect goods during storage and transportation: boxes, bubble wrap, and pallets.
Why is inventory management important for businesses?
Proper inventory management is vital for maintaining profitability and operational efficiency. Mismanaging inventory can lead to stockouts, lost sales, and unhappy customers. Conversely, overstocking can inflate costs and reduce cash flow.
A smooth inventory management process helps avoid these issues, optimising your supply chain, and supporting your business’s growth.
Real-world examples
Imagine you're a small retail business that sells handmade candles. You'll have to track raw materials like wax, wicks, and scents, as well as finished products. Effective inventory management helps you know when to reorder supplies, how much stock is on hand, and which products are selling well.
This reduces the risk of running out of popular items or holding too much unsold inventory, ensuring the business runs smoothly and profitably.
Now, let's take a look at a larger business.
Let's say you're managing inventory for a large electronics retailer. You'll need to track a vast array of inventory items, including raw materials like circuit boards and components, work-in-progress items such as partially assembled devices, and finished goods like smartphones and laptops.
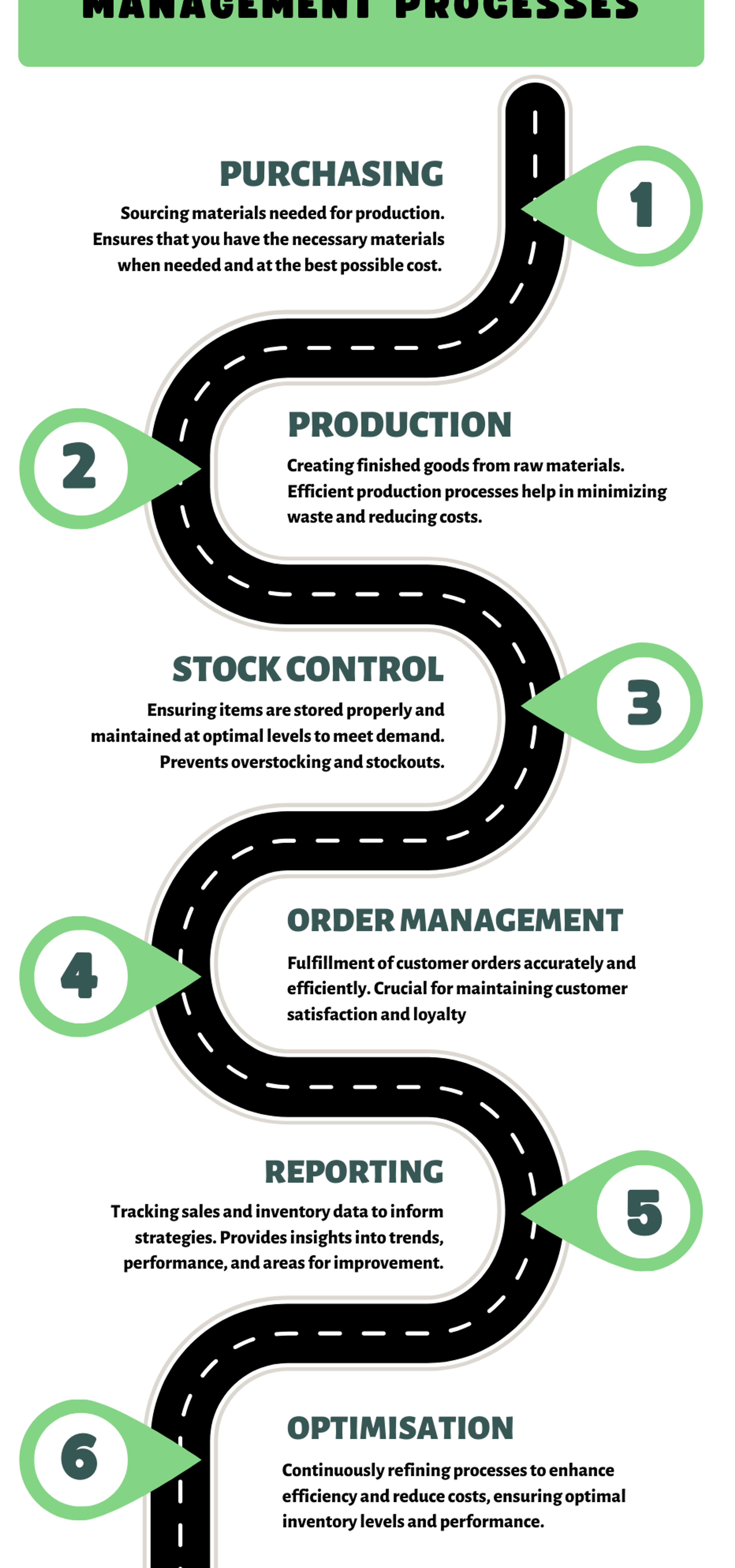
Periodic vs perpetual inventory management—What's better?
Periodic inventory management involves counting and updating inventory at set intervals, like weekly or monthly. It's simpler and cheaper, making it great for small businesses. However, it can be less accurate, leading to potential stockouts or overstocking between counts.
For example, a small bookstore might count its stock at the end of each month to update records and place orders.
Perpetual inventory management tracks inventory continuously in real-time. This method provides highly accurate, up-to-date inventory levels, reducing the risk of stockouts and overstocking. It is more complex and expensive to implement, requiring advanced software and technology.
For instance, a large supermarket uses barcode scanners at checkout and automated systems to instantly update inventory levels, ensuring they always know what's in stock.
What are some inventory management challenges?
- Inaccurate inventory data
- Errors in data entry or lack of real-time updates can lead to discrepancies between actual and recorded stock levels.
- Overstocking and understocking
- Maintaining the right balance of inventory is challenging. Overstocking ties up capital and increases holding costs, while understocking leads to lost sales and dissatisfied customers.
- Demand variability
- Fluctuations in customer demand can make it difficult to predict the right inventory levels, leading to either excess stock or stockouts.
- Supply chain disruptions
- Delays from suppliers, transportation issues, or geopolitical events can disrupt the supply chain, affecting inventory availability and delivery schedules.
- Inventory shrinkage
- Losses due to theft, damage, or administrative errors can reduce available stock, impacting overall inventory levels and profitability.
- Warehouse space limitations
- Limited storage space can make it challenging to manage and organise inventory efficiently, leading to operational inefficiencies and increased costs.
- Complexity in tracking multiple locations
- Managing inventory across multiple warehouses or retail locations adds complexity and can lead to inconsistencies in inventory records.
- Integration with other systems
- Ensuring seamless integration between inventory management software and other business systems like eCommerce platforms, accounting software, and CRM systems can be technically challenging.
- Cost control
- Balancing the costs associated with purchasing, storing, and managing inventory while maximising profitability requires careful planning and constant monitoring.
- Regulatory compliance
- Adhering to industry-specific regulations and standards for inventory management, such as tracking expiry dates for perishable goods or maintaining records for audit purposes, adds an extra layer of complexity.
How to create an inventory management plan
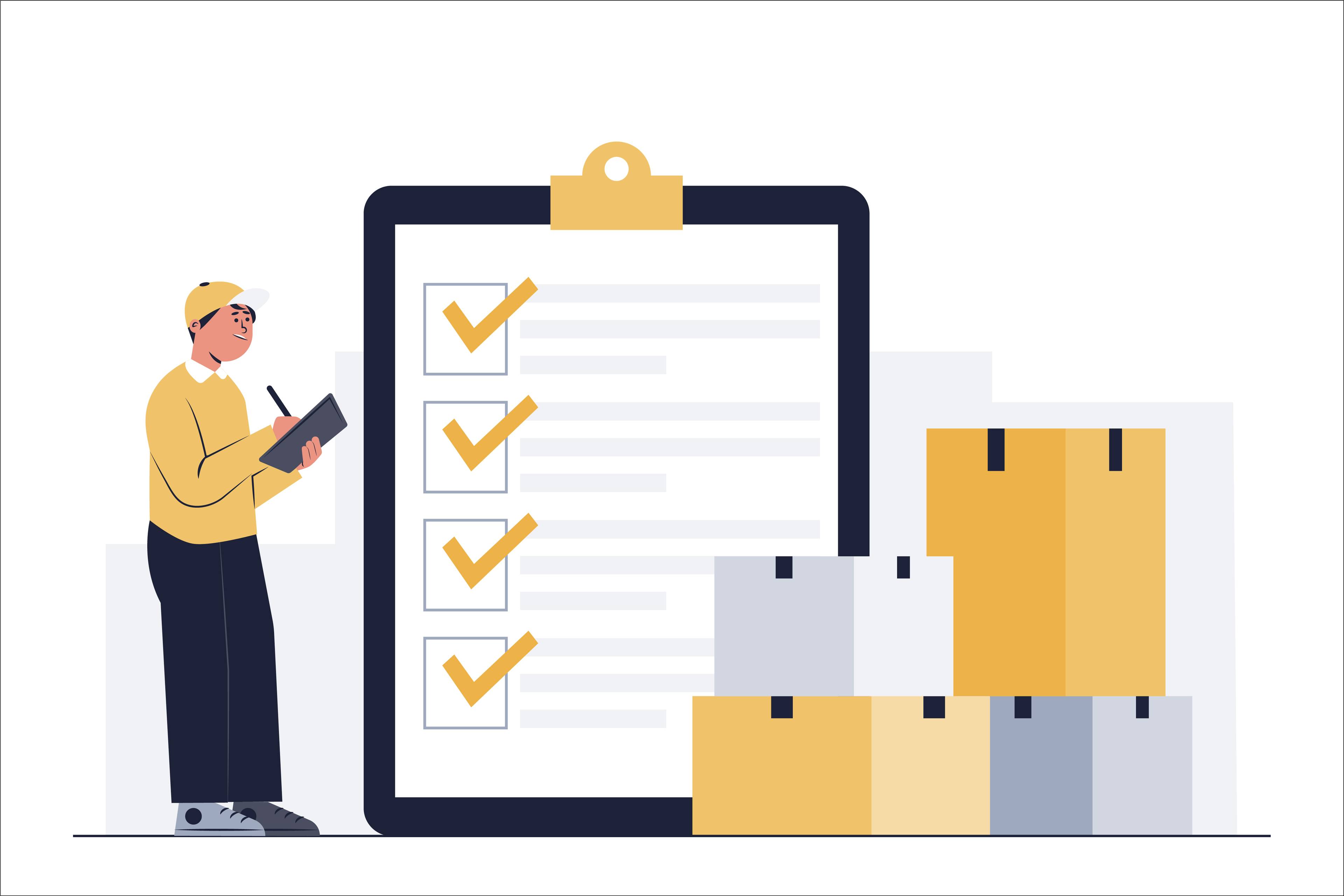
Creating an inventory management plan is essential for maintaining optimal stock levels and ensuring efficient operations. Follow these steps to develop a comprehensive plan:
1. Assess your current inventory
Start by conducting a thorough assessment of your existing inventory. Take an accurate account of stock levels (known as a "stock take"), categorise items, and identify any issues such as excess stock or frequent stockouts.
2. Define inventory goals
Set clear objectives for your inventory management. These might include reducing holding costs, improving order fulfilment times, or increasing inventory turnover.
3. Choose an inventory management system
Select a system that suits your business needs. Decide between periodic or perpetual inventory systems and consider investing in inventory management software to automate and streamline processes.
4. Establish reorder points and safety stock levels
Determine the minimum stock levels at which new orders should be placed (reorder points) and set safety stock levels to buffer against unexpected demand or supply chain disruptions.
5. Implement inventory control methods
Use methods such as ABC analysis, Just-in-Time (JIT), or Economic Order Quantity (EOQ) to manage your stock more effectively. These techniques help prioritise high-value items and optimise order quantities.
6. Develop standard operating procedures
Create detailed procedures for inventory-related tasks, including receiving, storing, and issuing stock. Standardising these processes ensures consistency and reduces errors.
7. Train your staff
Ensure that all employees involved in inventory management are well-trained on the new procedures and systems. Regular training sessions can help maintain high standards and improve efficiency.
8. Monitor and review
Regularly monitor inventory performance using key metrics such as inventory turnover, order accuracy, and stockout rates. Review your plan periodically and adjust it based on performance data and changing business needs.
Best practices in inventory management
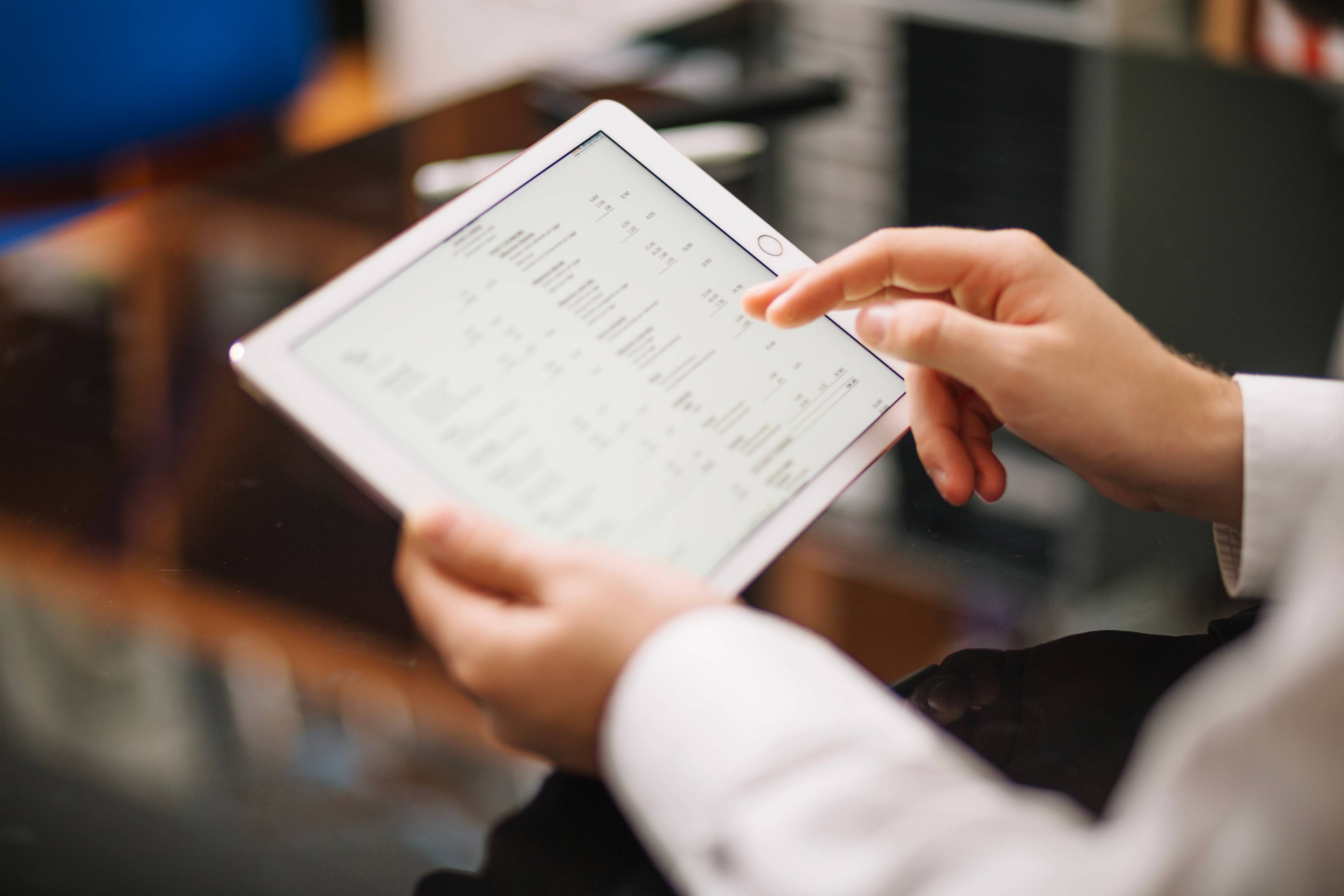
Categorise inventory correctly
Classify your inventory into categories like raw materials, work-in-progress, and finished goods. This helps you manage different types of inventory more effectively and ensures you have the right items available when needed.
Implement a perpetual inventory system
Use perpetual inventory systems to maintain accurate and real-time records of your stock. This inventory software automatically update inventory levels with each transaction, reducing the chances of errors and discrepancies.
Set optimal safety stock levels
Determine the appropriate amount of safety stock to keep on hand. This buffer stock helps you avoid stockouts during unexpected demand surges or supply chain delays.
Perform regular stock takes
Conduct regular physical inventory counts to verify that your records match the actual stock on hand. This practice helps identify discrepancies and ensures accurate inventory data.
Convert historical data into business intelligence
Analyse past inventory data to identify trends and make informed decisions. Use this information to forecast demand, plan inventory levels, and optimise purchasing strategies.
Maintain minimum inventory levels
Determine and maintain the smallest inventory levels required to meet customer demand. This approach minimises holding costs and reduces the risk of excess inventory.
Mitigate supply chain risks
Prioritise supply chain management to avoid potential mishaps. Develop strong relationships with reliable suppliers and diversify your supplier base to reduce dependency on a single source.
Track and improve inventory velocity
Monitor the speed at which inventory moves through your system. Improving inventory velocity helps reduce holding costs and ensures that products are available when customers need them.
9 Essential inventory management techniques
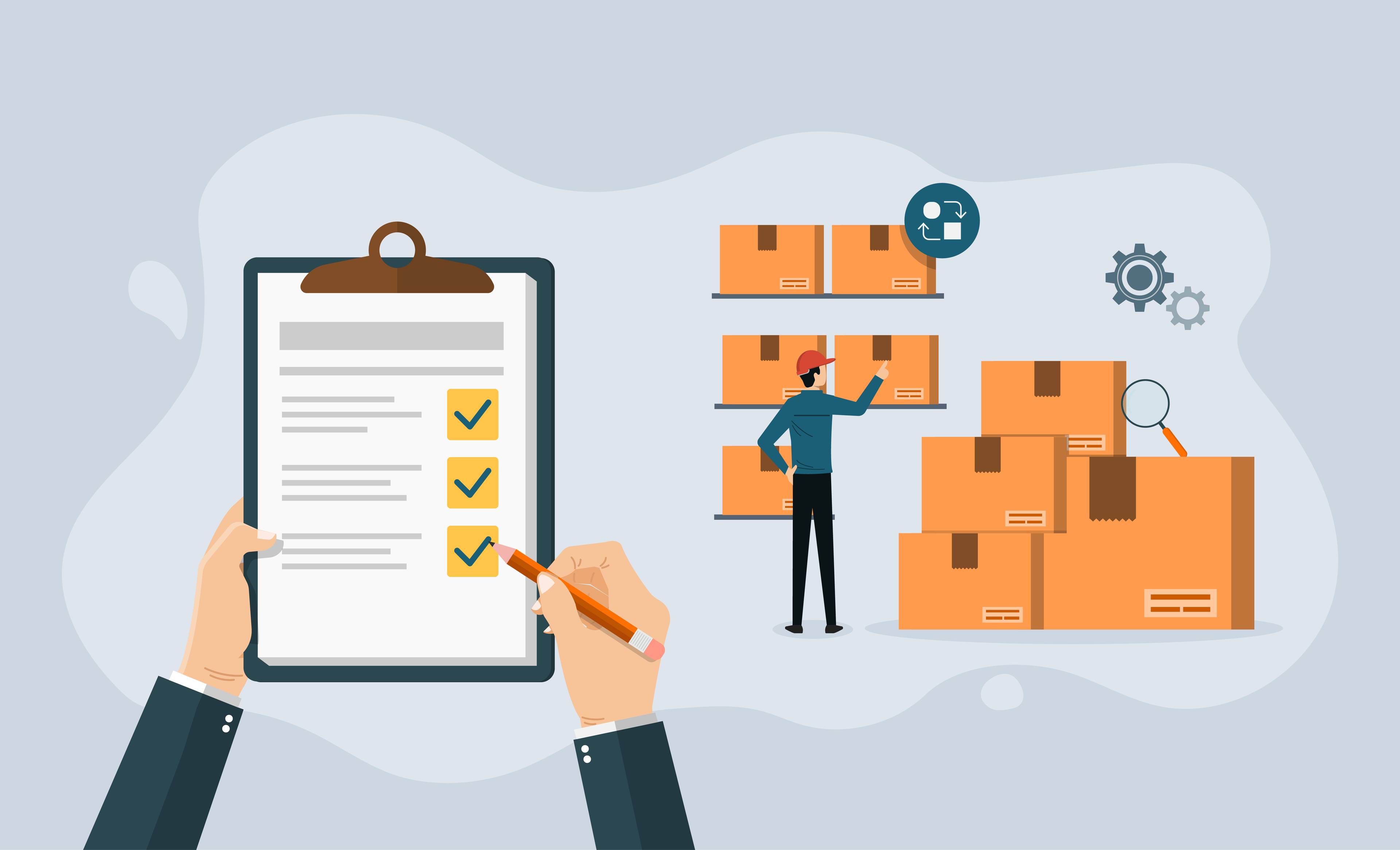
- Just-in-time (JIT) inventory – Ordering and receiving inventory only as needed for production and sales. It reduces holding costs but requires precise demand forecasting to avoid stockouts.
- Just-in-case (JIC) stock control – Maintaining high inventory levels to protect against unexpected demand surges or supply chain disruptions. It reduces the risk of stockouts but can tie up capital in unsold inventory.
- ABC analysis – This method categorises inventory into three classes: A, B, and C. Class A items are the most valuable and require careful management. Class B items are of moderate value, while Class C items are the least valuable. This technique helps prioritise resources and focus on high-value items.
- First in, first out (FIFO) and last in, first out (LIFO)– FIFO assumes the oldest inventory is sold first, which is useful for perishable goods. LIFO assumes the most recently acquired inventory is sold first. Each method affects accounting and tax calculations differently.
- Dropshipping– Products are shipped directly from the supplier to the customer. This reduces the need for holding inventory but can complicate quality control and customer service.
- Vendor-managed inventory (VMI) – Suppliers manage inventory levels for their customers. This approach can streamline replenishment and reduce stockouts, but it requires strong supplier relationships and trust.
- Cross-docking – Involves unloading goods from inbound trucks and loading them directly onto outbound trucks with minimal storage time. This technique reduces storage costs and speeds up delivery times.
- Cycle counting – The process of regularly counting a small subset of inventory. It helps maintain accurate inventory records without the disruption of full stocktakes.
- Economic order quantity (EOQ)EOQ is a formula used to determine the optimal order quantity that minimises total inventory costs, including holding and ordering costs. It helps maintain efficient inventory levels.
Long-term inventory strategies for success
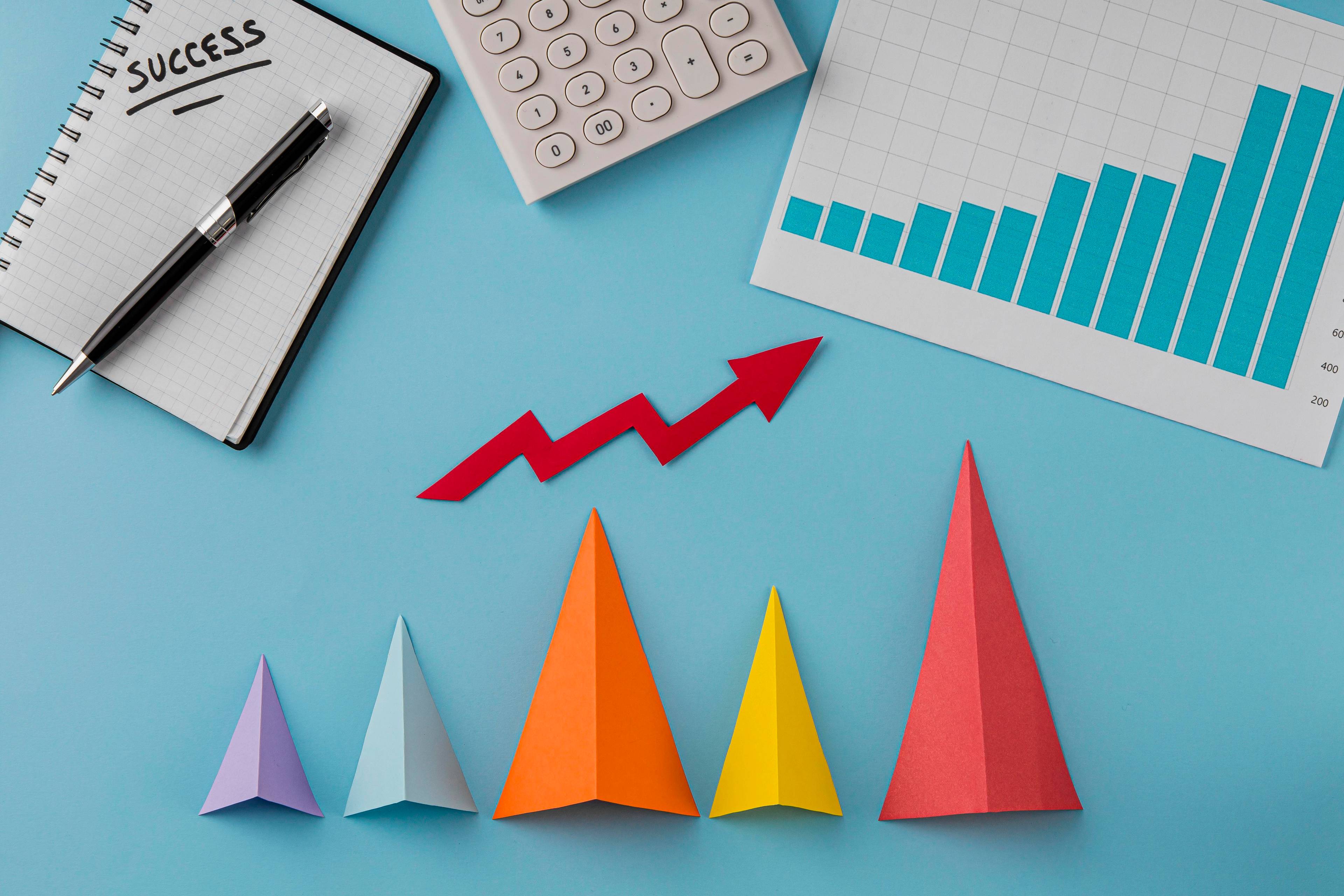
Demand planning
Predict future customer demand to align inventory levels accordingly. This involves analysing historical data, market trends, and seasonality to forecast demand. Accurate demand planning ensures you have the right amount of stock at the right time.
Inventory optimisation
Apply techniques to minimise costs while meeting customer demand. This includes setting optimal reorder points, maintaining safety stock, and using EOQ. Optimisation reduces excess inventory and stockouts, improving cash flow and operational efficiency.
Integration with other systems
Combine inventory management with ERP, CRM, and POS systems for a unified approach. Integration ensures real-time data sharing across departments, improving decision-making and operational efficiency.
Inventory turnover analysis
Track how often your inventory is sold and replaced over a period. High turnover rates indicate strong sales and efficient inventory management, while low rates suggest overstocking or weak demand. Use this analysis to adjust your inventory strategies.
Continuous improvement
Regularly review and refine your inventory management practices. Implement feedback loops, monitor performance metrics, and stay updated on industry best practices. Continuous improvement helps you adapt to changing market conditions and maintain efficient operations.
Useful tools and technologies
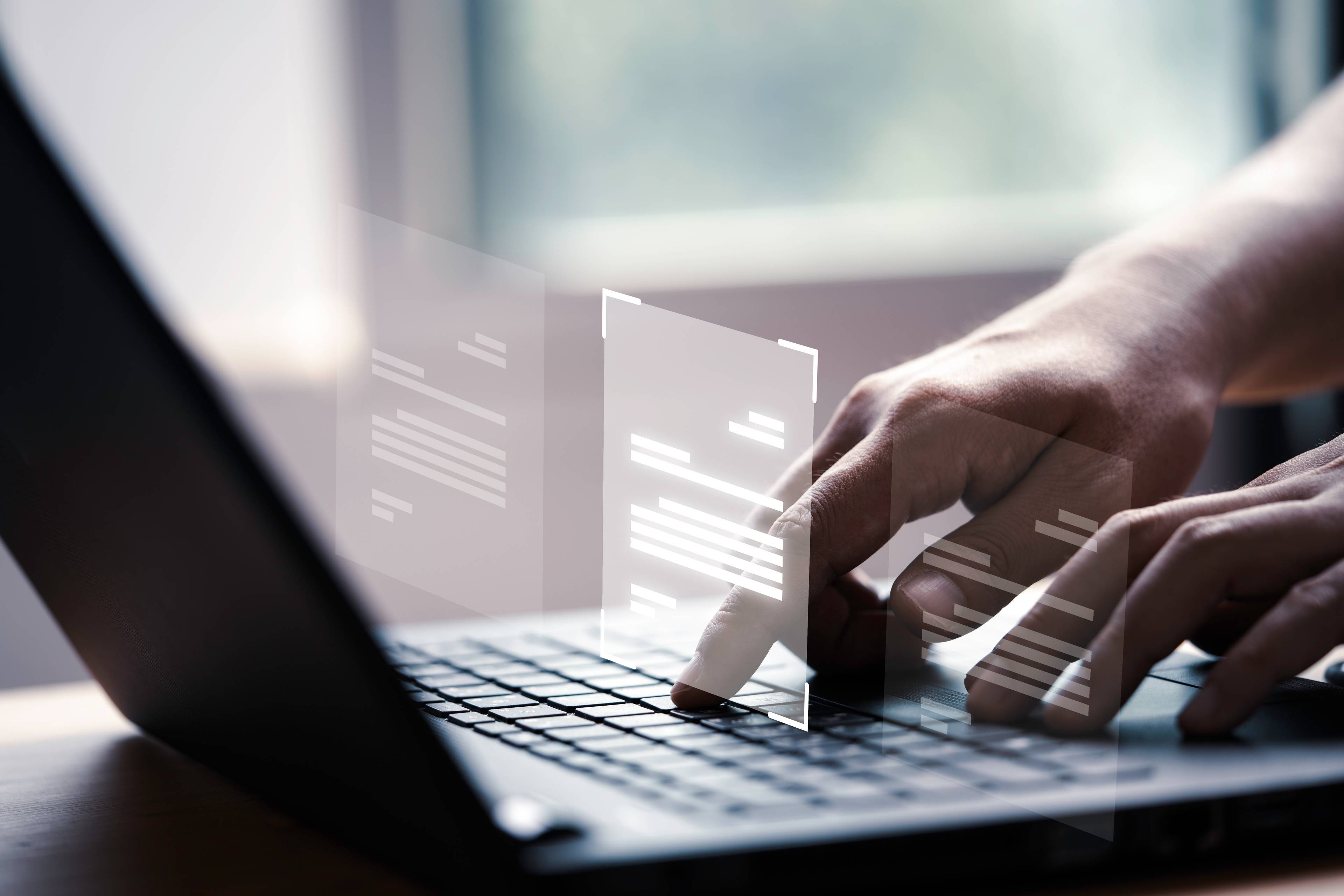
- Barcode scanners
- These streamline the processes of receiving, storing, and shipping, ensuring inventory records are always up-to-date.
- RFID systems
- Provide real-time tracking of inventory items, enhance accuracy and visibility, making stock management easier and reducing losses.
- Mobile technology
- Features like barcode scanning, inventory checks, and data updates can be accessed from anywhere, increasing flexibility and efficiency.
- Integration with POS systems
- Provides real-time updates on sales and stock levels. This prevents stockouts and overstocking by providing accurate data on inventory movement.
- Cloud-based solutions
- These eliminate the need for on-site hardware, allowing for scalable and flexible inventory management.
- Analytics and reporting tools
- These tools help identify trends, forecast demand, and make data-driven decisions to optimise stock levels and improve efficiency.
Many inventory management systems provide all of the above. Let's take a look at some of the most well-reviewed available on the market.
4 Popular inventory management systems
Efficient inventory management is greatly enhanced by using dedicated software solutions. These tools automate and streamline various processes, from tracking stock levels to forecasting demand. Here are a few of the best inventory management software options available:
Unleashed
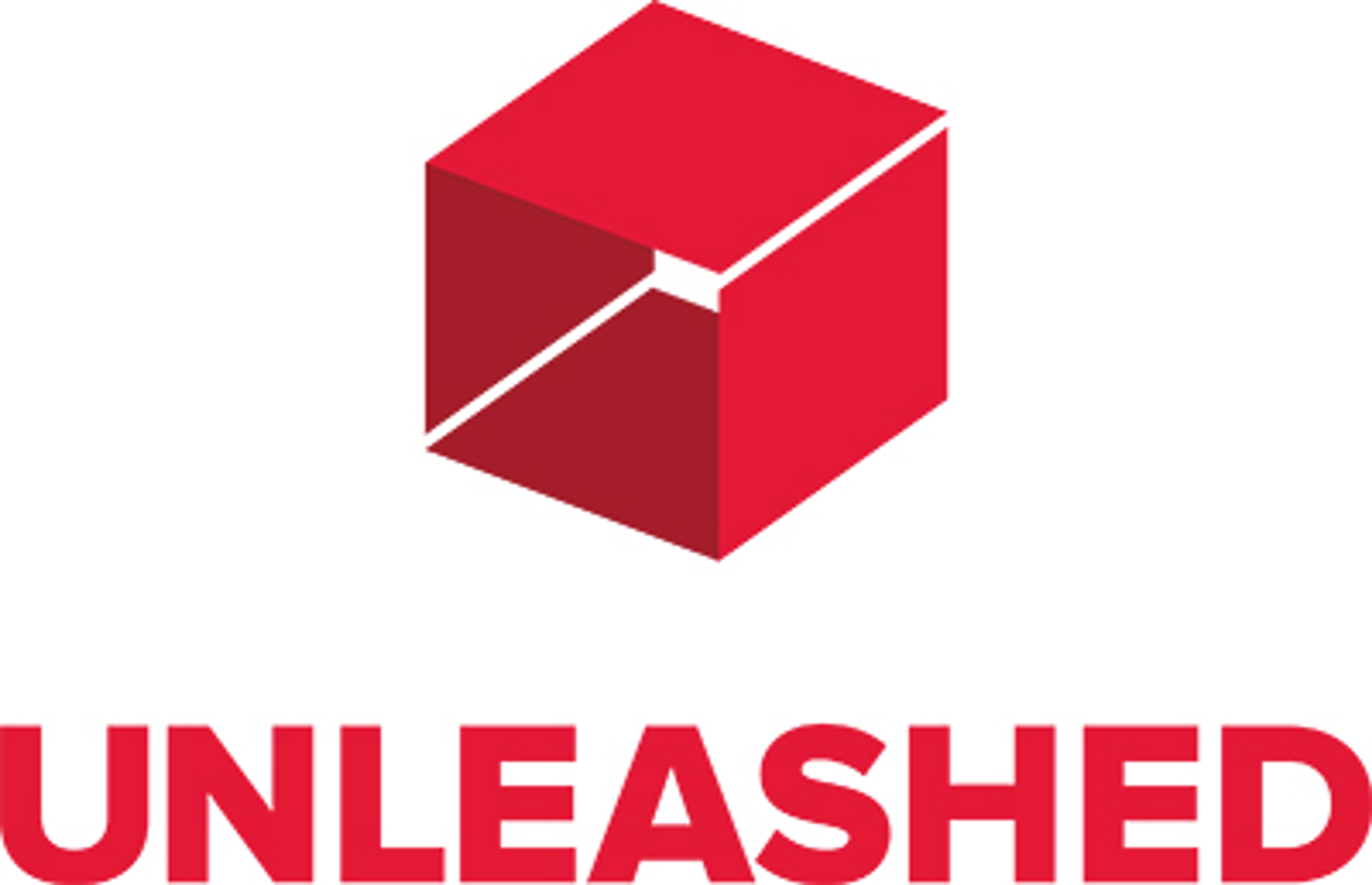
3.8/5 stars on G2
Best for: Versatile choice for manufacturers, wholesalers, and eCommerce retailers
Unleashed offers comprehensive features for managing inventory, including real-time stock tracking, order management, and detailed reporting.
- Real-time inventory visibility
- Integration with popular platforms like Shopify, Xero, and Salesforce
- Advanced reporting and analytics
- Batch and serial number tracking
- Barcode scanning and RFID support
- Mobile app for inventory management on the go
Pricing starts at $80 per month.
TradeGecko (QuickBooks Commerce)
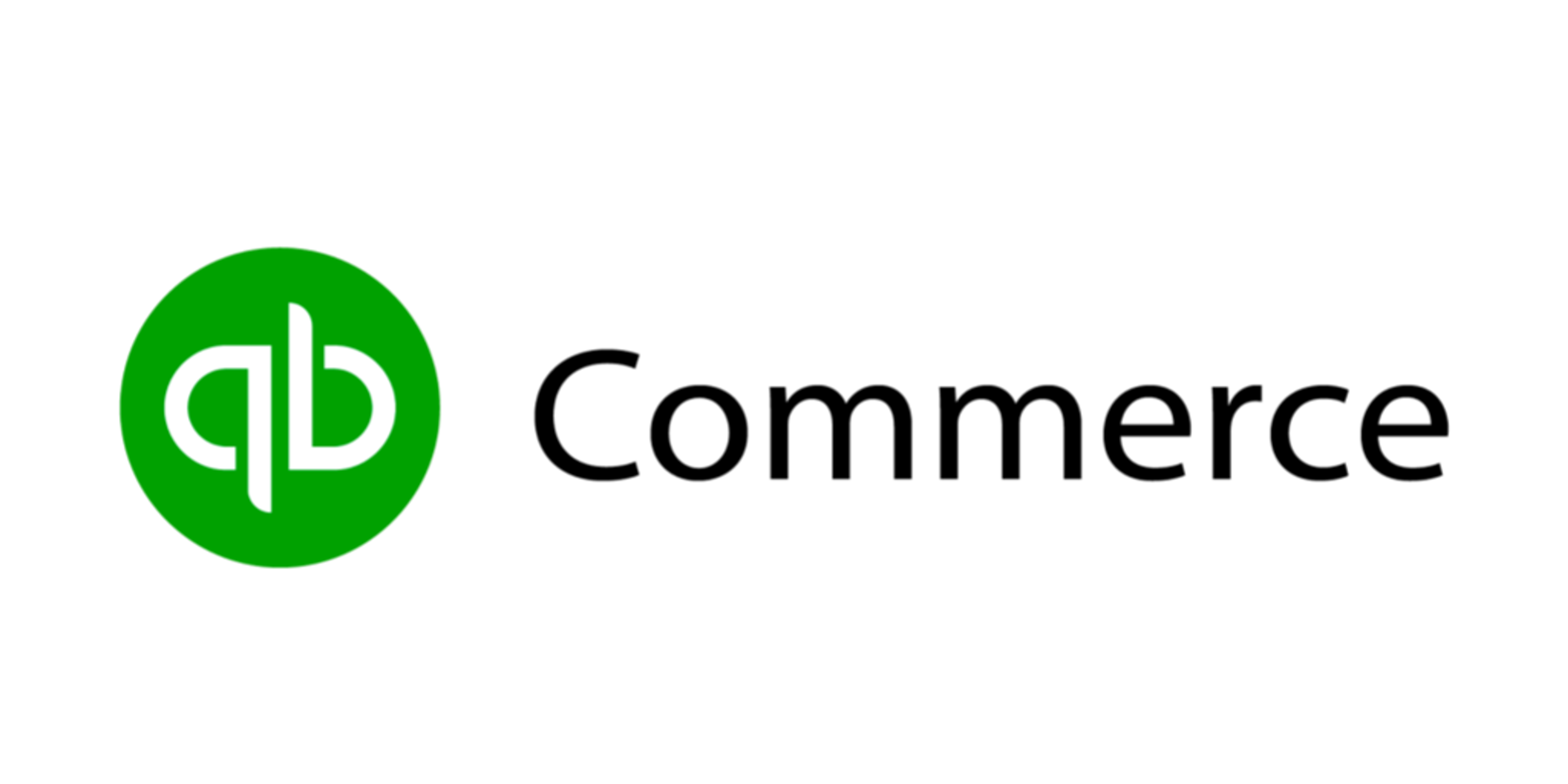
3.8/5 stars on G2 (QuickBooks)
Best for: Businesses seeking robust integration with their existing financial systems
TradeGecko, now part of QuickBooks Commerce, provides robust inventory management capabilities combined with powerful order management and sales analytics.
- Multi-channel sales management
- Automated stock adjustments and reordering
- Comprehensive sales and order analytics
- Integration with QuickBooks for seamless accounting
Pricing starts from £29 per month.
Cin7
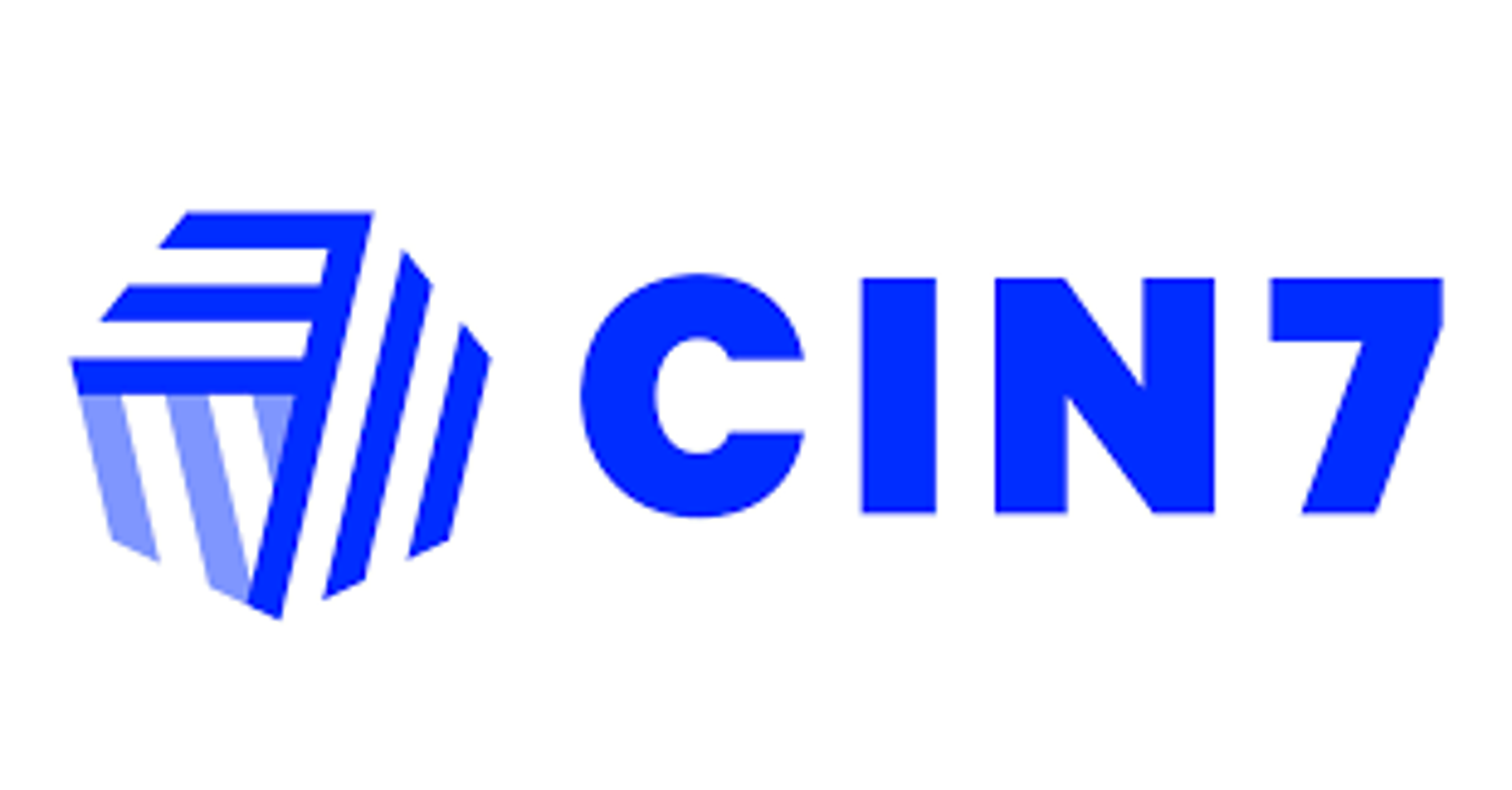
Best for: Wholesalers and large enterprises operating in multiple locations
Cin7 is a cloud-based inventory management system designed to streamline operations across multiple sales channels.
- Centralised inventory control for multiple locations
- Integrated POS and eCommerce solutions
- Automated purchase orders and stock transfers
- Real-time stock level updates and tracking
14-day free trial available. Pricing starts from £270 per month.
Zoho Inventory
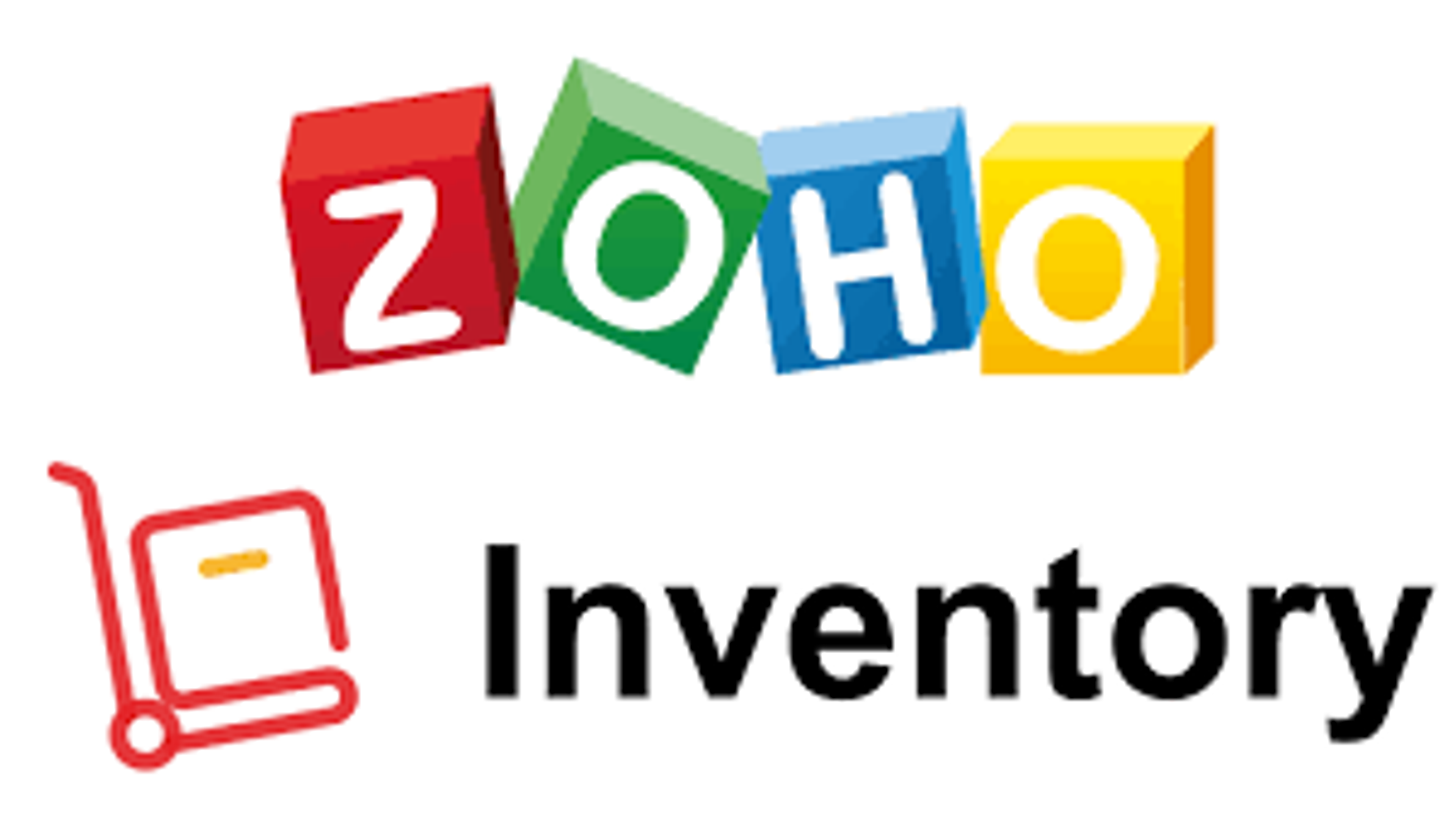
4.4/5 on G2
Best for: Growing businesses who want to scale easily
Zoho Inventory is a cost-effective solution for small to medium-sized businesses. It offers essential inventory management features along with integration with other Zoho products and popular eCommerce platforms.
- Multi-channel inventory management
- Automated workflows for order management
- Integration with Zoho CRM and Zoho Books
- Detailed inventory and sales reports
Pricing from £25 per month.
Struggling with your inventory management? Leverage business storage
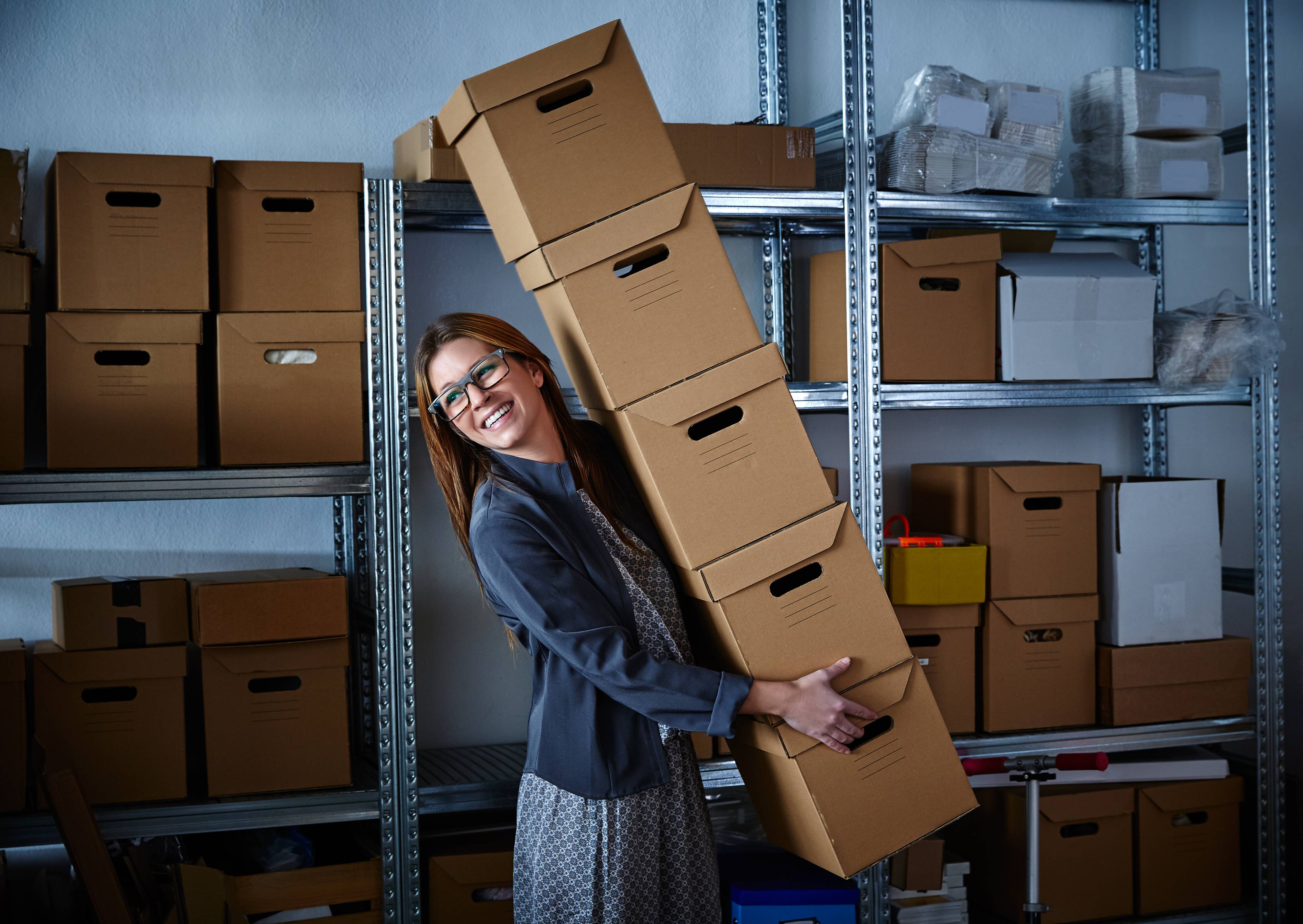
For many small businesses, finding enough space for stock can be challenging. Using self storage can be a cost-effective way to manage your inventory efficiently. This enables you to focus on what matters most: growing your business.
Business storage solutions (like those offered by HOLD) provide the flexibility to adjust your storage space based on inventory needs. During peak seasons or fluctuating demand, having the option to scale your storage up or down is invaluable.
Renting storage space with us is more affordable than maintaining your own warehouse. In fact, you may be better off checking out our own great value warehouse storage. With HOLD, you only pay for the space you use, reducing overhead costs and freeing up capital for other areas of your business.
We're proud to present our brand new business rooms in Kings Cross London. With the option for climate control, these have robust security measures, including 24/7 surveillance and secure access controls.
We also provide 24/7 access, allowing you to retrieve or store stock at any time. The cherry on top? You can also run your business from one of our units!
Feel free to use our unit size calculator (we offer small units up to warehouse size) and contact us for a no-strings quote.
Frequently Asked Questions
What security measures does HOLD have in place for its business storage units?
At HOLD, advanced security measures are essential for protecting our customer's business assets. The features we offer include:
- 24-hour CCTV
- Individually alarmed units
- Secure loading bay
- Robust security for individual units
- Personal pin codes
- Fire detection systems
These features not only provide peace of mind, but also protect your business assets from potential threats.
Which inventory system is best for small business?
For small businesses, a perpetual inventory system is often best. It provides real-time tracking of stock levels, reducing errors and improving efficiency. Systems like QuickBooks Commerce and Cin7 are popular choices due to their user-friendly interfaces and integration capabilities
What are the four main steps in inventory management?
The four main steps in inventory management are:
- Purchasing: Acquiring the necessary stock from suppliers.
- Production: Converting raw materials into finished goods.
- Stock Control: Managing and maintaining optimal inventory levels.
- Sales and Reporting: Fulfilling customer orders and tracking inventory data to inform business decisions.
What is the stock position in inventory management?
This refers to the current quantity of inventory items available for use or sale at any given time. It includes all types of inventory such as raw materials, work-in-progress, and finished goods.
What is a stock out in inventory management?
This occurs when an item is not available for sale or use because the inventory has been depleted. This situation can lead to lost sales, dissatisfied customers, and production delays.